Fasteners and Machining: Simplifying the Production Refine
Fasteners and Machining: Simplifying the Production Refine
Blog Article
Navigating the Globe of Fasteners and Machining: Methods for Accuracy and Speed
In the detailed world of fasteners and machining, the quest for precision and rate is a continuous difficulty that demands precise interest to detail and calculated planning. From comprehending the diverse range of fastener types to selecting ideal products that can endure rigorous needs, each step in the process plays an essential duty in accomplishing the preferred result.
Understanding Fastener Types
When picking bolts for a project, comprehending the various types offered is crucial for making sure optimal performance and dependability. Bolts are made use of with nuts to hold materials with each other, while screws are versatile fasteners that can be made use of with or without a nut, depending on the application. Washers are crucial for distributing the lots of the fastener and stopping damages to the material being secured.
Picking the Right Products
Understanding the value of selecting the best materials is extremely important in ensuring the ideal efficiency and integrity of the picked bolt types talked about formerly. When it involves bolts and machining applications, the material selection plays a vital duty in establishing the total strength, sturdiness, rust resistance, and compatibility with the desired setting. Various materials offer varying buildings that can considerably affect the performance of the fasteners.
Typical materials utilized for fasteners include steel, stainless steel, aluminum, brass, and titanium, each having its special staminas and weaknesses. Steel is renowned for its high strength and resilience, making it appropriate for a large range of applications. Stainless steel provides excellent corrosion resistance, perfect for settings susceptible to moisture and chemicals. Aluminum is corrosion-resistant and lightweight, making it ideal for applications where weight decrease is vital. Brass is commonly selected for its aesthetic allure and exceptional conductivity. Titanium is known for its outstanding strength-to-weight ratio, making it perfect for high-performance applications. Selecting the appropriate material involves taking into consideration aspects such as toughness needs, environmental problems, and spending plan constraints to ensure the preferred performance and long life of the fasteners.
Precision Machining Techniques
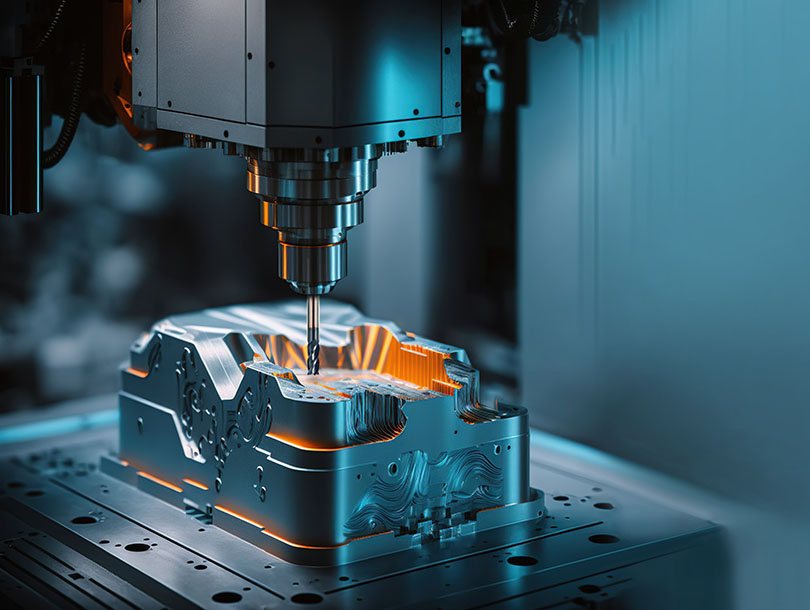
In addition to CNC machining, other accuracy techniques like grinding, transforming, milling, and exploration play important duties in fastener manufacturing. Grinding helps accomplish great surface finishes and tight dimensional tolerances, while transforming is frequently utilized to develop cylindrical parts with exact sizes. Milling and drilling operations are crucial for shaping and producing openings in bolts, ensuring they satisfy specific specifications and function properly.
Enhancing Rate and Efficiency
To enhance bolt manufacturing processes, it is crucial to enhance operations and carry out efficient approaches that complement accuracy machining techniques. Automated systems can manage repetitive jobs with precision and speed, permitting workers to concentrate on more complicated and value-added tasks. By incorporating these methods, manufacturers can accomplish an equilibrium between rate and accuracy, ultimately improving their competitive side in the anchor bolt industry.
Top Quality Control Measures
Applying strenuous top quality control steps is vital in making sure the dependability and uniformity of bolt items in the production process. Fasteners and Machining. Quality control measures include different phases, beginning from the option of raw materials to the final inspection of the finished bolts. This involves assessing variables such as material strength, longevity, and make-up to assure that the fasteners fulfill market criteria.
Regular calibration of tools and machinery is essential to keep consistency in production and make certain that fasteners satisfy the needed resistances. Implementing stringent protocols for recognizing and resolving non-conformities or problems is important in avoiding substandard products from entering the market. By developing an extensive quality assurance framework, suppliers can copyright the track record of their brand name and supply bolts that satisfy the greatest standards of efficiency and durability.
Final Thought
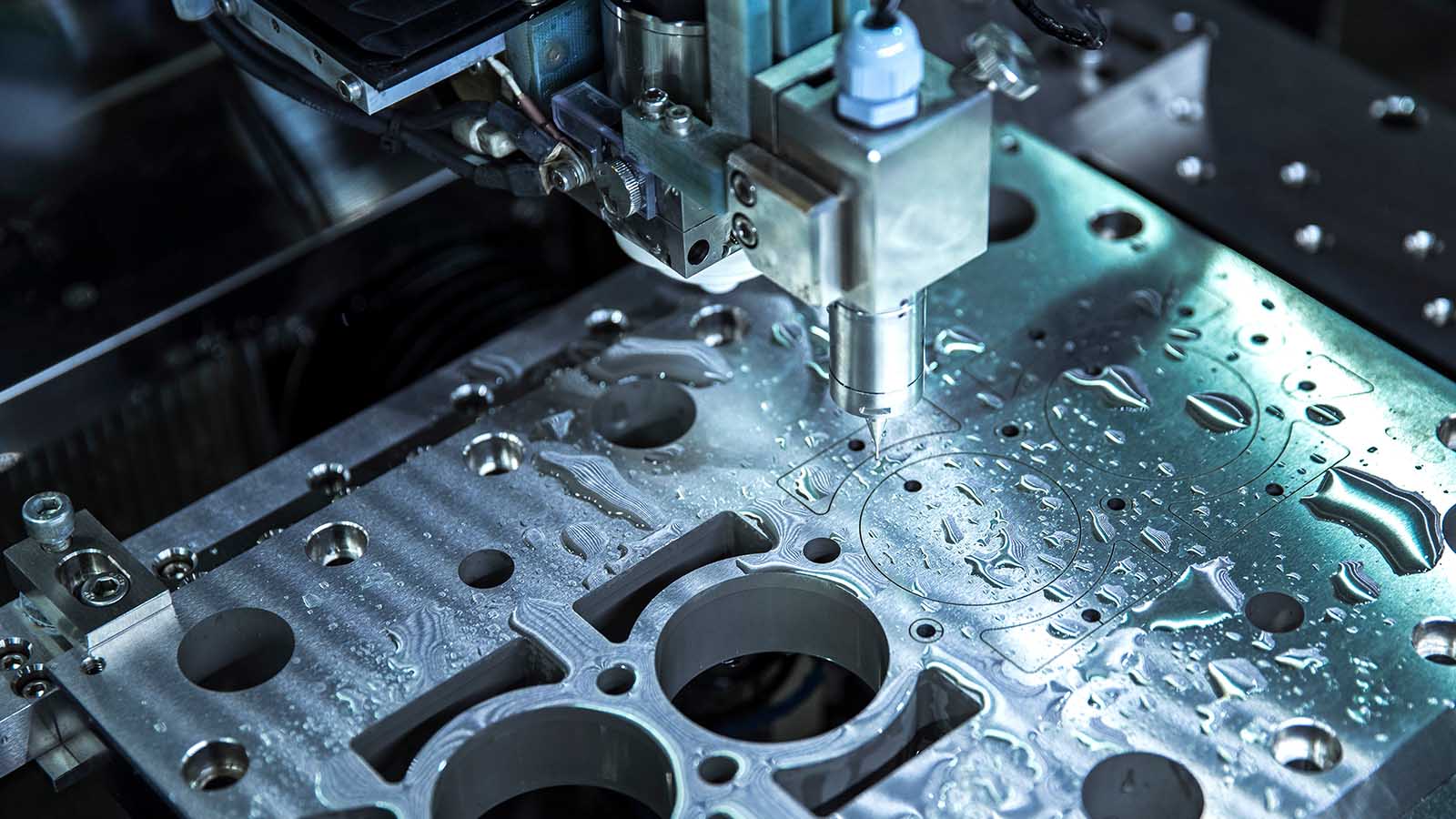
In the complex world of fasteners and machining, the pursuit for precision and rate is a continuous obstacle that requires thorough focus to detail and calculated planning. When it comes to fasteners and machining applications, the material choice plays an important duty in identifying the general strength, durability, deterioration resistance, and compatibility with the intended atmosphere. Accuracy machining includes different innovative approaches that make certain the limited tolerances and specifications required for bolts.In site here enhancement to CNC machining, other precision strategies like grinding, transforming, milling, and boring play vital duties in bolt manufacturing.To optimize fastener production procedures, it is crucial to streamline procedures and implement effective approaches that match precision machining methods.
Report this page